Products
Contact Us
- Address:Suite 807, TianAn Hi-tech Development Plzaza. No.555 North PanYu Road, PanYu DistrictGuangZhou, China.
- Tel:020-39211238
- Fax:020-39211286
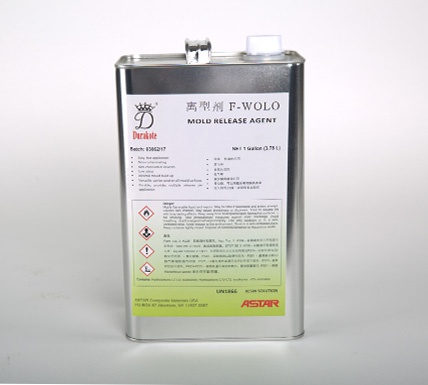
Durakote F-WOLO
Brands:Durakote
Types:
Field of application:
Introduction:Durakote F-WOLO is designed to release glass reinforced polyester(GRP) or vinly ester, phenolic or epoxy components from composite or metal moulds and is ideally suited for high gloss applications. Durakote F-WOLO is an advanced polymeric resin in a non-chlorinated organic solvent blend. Durakote F-WOLO gives an instant with high gloss surface by simple wipe application; there is no need rubbing or polishing. The Durakote F-WOLO is extremely durable and capable of giving many releases per application. It will not contaminate the released surface.
Product Benefits |
Physical Properties |
l Fast, easy wipe application l Non contaminating l Non-chlorinated solvents l Low odour l Multiple mould build-up l Durable; provides multiple release per application
|
Appearance - Clear, colourless liquid Odour - Hydrocarbon Specific Gravity - 0.729 g/cc Solvent - Aliphatic hydrocarbon Coverage -100-125 m2/L per coat Shelf Life - One year Storage - Flammable store(see MSDS) |
Note:
The polymeric resin used in Durakote F-WOLO reacts with moisture. Please ensure can is resealed after each and every use. Durakote F-WOLO is supplied ready to use, no shaking or mixing is required. Do not mix with other products or solvents. Store in original container in approved flammables store.
Application:
Please read Safety Date Sheet before use.
If necessary polish mould to desired level of gloss. If a wax or silicone based release agent had been used previously, remove traces of wax using a solvent based cleaner such as Durakote PMC-600.Durakote W-WOLO can be applied over existing semi-permanent release agents without a further cleaning step. However the mould should be clean and dry before use. Mould cleaning and release agent application should be performed in a well-ventilated area
1.Apply DurakoteF-WOLO to clean, dry cotton cloth. Do not over-apply; the cloth must not be soaked or dripping.
2.Wipea thin film of F-WOLO over mould surface covering an area of approximately 1 m2. Vigorous rubbing or polishing is not required. The film should stay wet for up to 2 minutes(see over-leaf for further details)
3.Repeat steps 1 and 2 until the mould is completely coated. Ensure a good overlap with the previous area to provide complete coverage
4. When dry, allow a further 5-10minutes between coats for the film to partially cure
5. Repeat step 1-4 above for a further 2 coats (3 in total)
6.NOTE:for new or porous moulds, or repaired areas on old moulds, apply a further 2 coats (5 in total).A separated mould
sealer is not necessary.
7.When dry, allow final film to cure for at least 15minutes at room temperature before moulding. Allowing a longer cure or
heat curing (e.g. 5 min at 60℃) will improve film durability.
Please see over for further application details.
Reapplication:
When the release becomes hesitant, reapply one coat of Durakote W-WOLO in the same manner as described above.
Again allow a minumum of 15 minutes before commencing production. Ofter, reapplication is only required in high abrasion
areas such as external corners and vertical surfaces.
Note:
Use the tape-test before and after F-WOLO application. This will initially ensure the mould is clean and latterly, will ensure correct-F-WOLO coverage and cure time have been observed and that the coating is ready for production. If the tape release is hesitant after F-WOLO application, simple apply another coat in the same manner as described above.
If the film appears hazy, it is likely that too much has been applied. DO NOT polish out the haze with a dry cloth. To remove the haze, re-apply a further thin coat of F-WOLO. Check product coverage and dry time. Frequently replace the cloth(this avoids product drying on the cloth after excessive use).
Please dispose of used cloths in the appropriate manner, Remember , wet cloths still contain highly flammable solvent.
Troubleshooting:
Problem |
Cause |
Solution |
Streaking
|
Cloth has picked-up dirt from the mould - poor cleaning prior to application
F-WOLO has dried on the cloth
|
Discard old cloth and replace with new. If necessary repeat mould cleaning process using Durakote PMC-600 prior to applying Durakote F-WOLO. Pay particular attention to cleaning mould flanges (edges.)
Discard old cloth and replace with new. Reapply F-WOLO and continues as normal. |
Hazing |
Over application
Configuration of mould - poor air circulation in mould well prevents the quick dry of F-WOLO ( improtant to generate a high gloss finish). Solvent vapours are heavier than air and will stay in mould well or cavity until removed. This is observed by a drastic increase in dry time( e.g. >>2 minutes which , in turn, cause hazing of the film.) |
Squeeze out cloth prior to use (over absorbent material). If product drips from cloth then too much has been applied to cloth. Discard old cloth and replace with new. Ensure dry time is <2 minutes. Ensure good air circulation over mould. Angle the mould to allow solvent vapour to drain out of the mould well. Alternatively, Use a fan to increase air flow over the mould (Placed in an appropriate position to blow across the mould). When using a fan, it is important that dust is not blown onto the muold.
|
Poor durability |
Durakote F-WOLO container has been left open for a extended period
|
Ensure can is resealed after each and every use . Replasewith fresh product.
|
Poor /tight release |
Highly porous moulds
|
F-WOLO is designed to be applied to high gloss gel coated moulds. The surface porosity of these moulds will be relatively low. For matte finish or highly porous moulds, an alternative product may be more appropriate. Please consult a Technical Representative
|
Mould hazes after first release |
Green mould. The mould has not been allowed to cure for the period specified by the gel coat/ resin |
Allow mould to cure for gel coat/ resin manufacture's recommended cure time(typically 2-3 weeks) before using. If any colour is removed during the cleaning process, I.e discolours the cloth, this is a good indication of a soft or green mould. |
GRP moulding outside the usual 15- 35 range
GRP mould outside the usual 15-35℃ range has many other detrimental effects, not just on the release agent, For example, gel coat application below 15℃ many result in permanent under cure. The further from this ideal temperature range that moulding is performed, the highly the risk of problems occurring. Please observe the recommendations of the gel coat and / or resin manufacture(s) with respect to the use of their products at these temperatures.
Although the recommended application temperature for F-WOLO is also between 15-35℃, the product may be used out side this range providing the following precautions are abserved.
Below 15℃
● An extra coat of F-WOLO is advised, i.e. 4 coats for old moulds. 6 coats for new moulds.
●Ensure that temperature of the F-WOLO is the same as that of the mould (to avoid condensation), I.E store the can and
the mould inside.
● Extra time should be allowed between coats; for example. at 10℃, allows a minimum of 30 minutes before the next
coat is applied.
●Extra time should be allowed for the final cure; for example at 10℃, allows a minimum of 60 minutes before
starting production. An over-night cure is recommended.
●The slower drying time of F-WOLO means that greater care is required not to over apply.
Above 35℃
● Greater care is required to ensure the cloth does not dry- out; i.e. reapply the product frequently
●One less coat is recommended , i.e. 2 for old moulds and 4 for new moulds and repaired areas.
●Ensure the use of the recommended cloths, I.E. Kimberly-Clark Wipe All x 60.
●Frequently replace the cloth (this avoids product drying on the cloth after excessive use)
If in any doubt, please contact a Technician at the n\umber below.